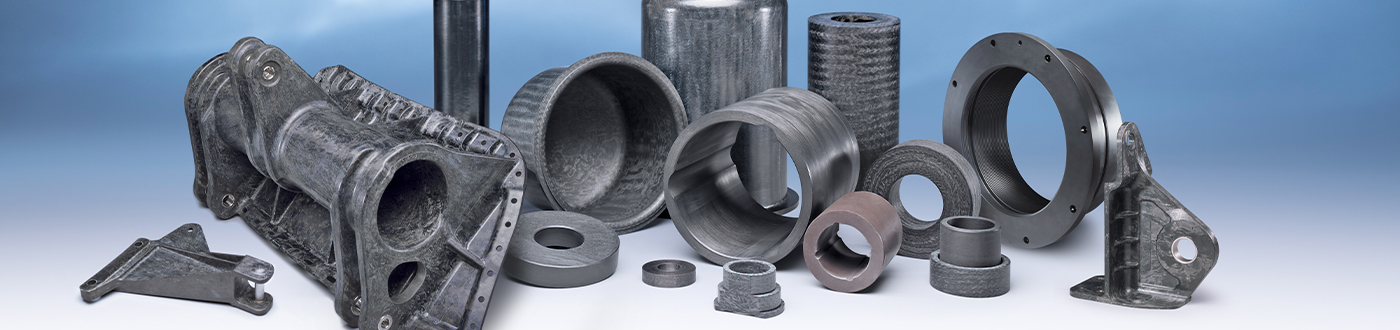
You are here:
Products
Need help with a product?
Get in touch
Call 1300 798 279 (from Australia)
+61 8 9251 1688 (outside Australia)
OR send us your enquiry
Xycomp® DLFTM
High performance thermoplastic composite
Xycomp® DLFTM is a lightweight thermoplastic composite developed to replace complex-shape metal components for a variety of industries. With outstanding fatigue, vibration and impact resistance, it provides up to 35% weight savings to help reduce emission, offers fuel savings while providing exceptional performance.
Xycomp® DLFTM is produced from aerospace-grade, carbon fiber reinforced, unidirectional prepreg tape which is chopped into flakes. This results in high fiber content (70% by weight), longer fibers (0.5 in./13 mm or greater), and a high degree of material control.
Flakes are matched-die compression molded in a proprietary process called ProFusion®, enabling the production of 3-D shapes with variable wall thickness and molded-in features such as fasteners, inserts, and ribs. The benefits of this molding technique include the consolidation of complex assemblies into fewer parts, and the optimization of raw material required per component (buy-to-fly ratio). In addition to these properties, Xycomp® DLFTM is resistant to all common aerospace fluids.
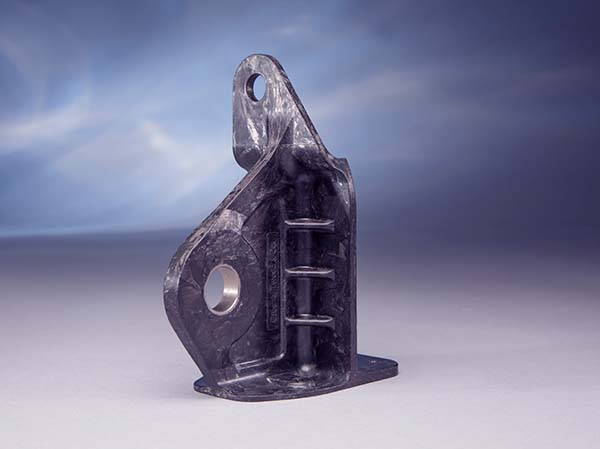
KLINGER is the authorised Australian distributor of Greene Tweed products.
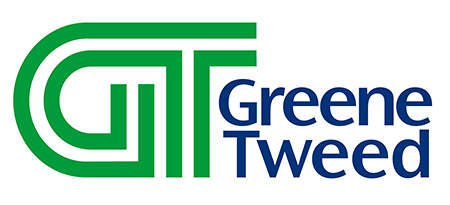
Xycomp® DLFTM components pass both FST (flame, smoke, toxicity) standards and the 15-minute burn-through requirement, making them ideal for use in aircraft interiors, engines, nacelles, or aerostructures. Through investment in extensive technical capabilities, Greene Tweed partners with customers from concept and design analysis, through certification, to production. Xycomp® DLFTM components are manufactured with nearly zero waste and are fully recyclable at the end of their service life.
Download Product Documents
Below you can find more product-related Information on Xycomp® Composites, free to access and download.
Applications
Nacelle and engine components, aircraft interiors, aerostructures.
Features and Benefits
- Up to 60% weight reduction compared to metal components, for reduced fuel burn
and emissions - ProFusion® near-net compression molding enables consolidation of complex assemblies
into fewer parts, with high quality and repeatability - Exceptional fatigue, vibration and impact resistance delivers performance equal to
or better than metal • Significant improvements in impact & elevated temp performance vs. injection-molded materials - Excellent retention of properties after thermal aging
- Chemical resistant to all common aerospace fluids
- Components are manufactured with nearly zero waste and are recyclable at the end of
their service life