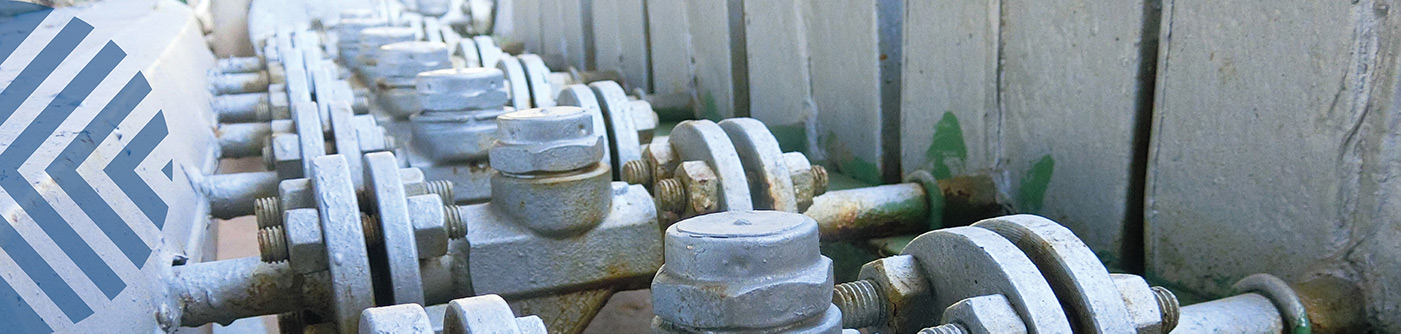
- KLINGER Australia
- Blogs
- Consequences of Malfunctioning Steam Traps
7 CONSEQUENCES OF MALFUNCTIONING STEAM TRAPS
The steam trap is an essential part of any steam system. It is the crucial link between good steam and condensate management. It retains steam within the process for maximum utilisation of heat, while releasing condensate and incondensable gases at the appropriate time. When steam traps aren’t functioning efficiently the following seven consequences may arise.
Safety concern for plant personnel and equipment
Environmental standard reductions/negative effect on CO2 emissions
Negative impact to plant systems and fuel consumption
Water hammer
Pressure surges/ steam line rupture.
Increased maintenance costs and energy bills
Excessive abrasion of valves and control valves
Steam installations have become more efficient by investing in the use of, for example, residual heat. Nevertheless, a lot of energy is still lost in the system due to (mainly small) leakages in steam traps.
When steam has dissipated its heat, the steam traps ensure that the condensate is quickly drained while the steam remains in the system. To minimize steam/energy losses, we recommend that you check your steam traps annually and exchange them if necessary.
We know that if routine inspections are not carried out, the underlying failure rate of steam traps is anywhere between 15% to 20% per year.
At 10 bar steam pressure, one 25mm (1”) steam trap leaks about 10 to 15 kg of steam per hour, which at a steam price of approximately $25 per tonne amounts to a cost of approximately $3,000 per year.
A steam leak results in a higher steam consumption. This ultimately also leads to a higher energy bill and has a negative effect on your CO2 emissions.
Prevent loss that occurs through Leaking Steam Traps
Through years of experience in steam technology, KLINGER offers you the specialist knowledge that is necessary for a project-based approach to controls. We do this through our KLINGER Atmeco Integrity Services division, the leader in asset integrity and emission management solutions across Australia, Asia Pacific and beyond.
KLINGER Atmeco Steam Loss Survey is typically conducted in six phases:
Phase 1: Preparation of a Steam Loss project
Phase 2: Database preparation
Phase 3: Source inventory
Phase 4: Unit monitoring phase
Phase 5: Reporting
Phase 6: Project closing
Based on the output of the reporting information, a repair program can then be put in place to rectify leaks. The achieved savings of raw materials can be huge and considerably higher than the total steam loss survey and repair costs.
Over the years, our team has pinpointed leaks equal to individual steam trap loss of more than 200 tons per year!
Read more about the benefits and methodology of our steam trap survey .
Steam Loss Survey
Share this article on social
Read related blogs
Have any queries?
Get in touch with KLINGER Atmeco; the leading service provider of end to end emission management and asset integrity solutions.
Call 1300 798 279 (within Australia)
+61 8 9251 1600 (outside Australia)
OR send us your enquiry