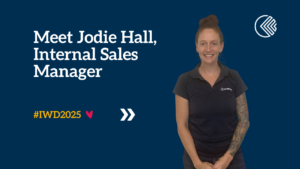
- KLINGER Australia
- Blogs
- Rising to the Challenge: Delivering Custom Gaskets for a Damaged Flange in Record Time
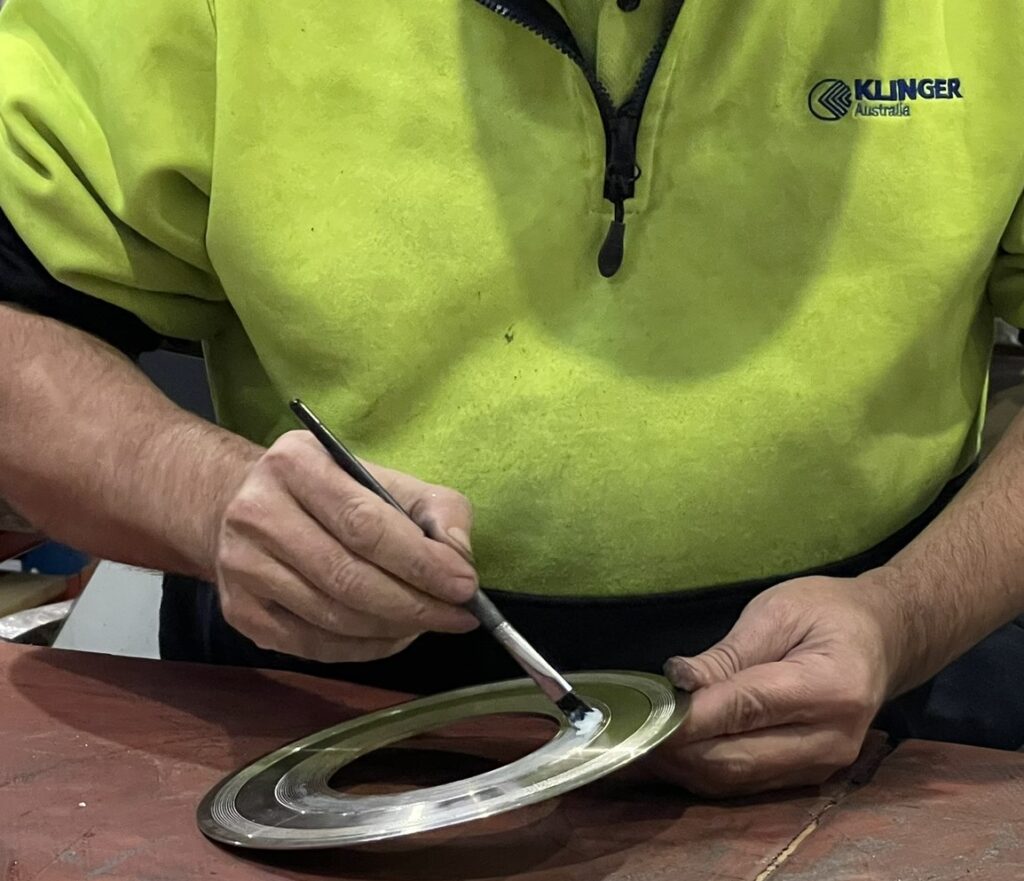
Fact box:
Custom-Engineered Solution: We designed a bespoke gasket to tackle a critical challenge.
Fast Turnaround: From design to delivery, the entire process took less than a day.
Cost and Time Savings: The quick delivery and installation of the gasket helped the client avoid significant downtime and the need for more expensive repairs, with perceived cost savings include daily production loss during shutdown, production loss savings, over-run/downtime costs and hand delivery versus hot shot services.
Total savings estimated: >$500,000
A major chemical processing plant recently faced an unexpected shutdown due to a damaged flange groove. The damaged flange was unsealable with standard gaskets, and conventional repair options—such as welding, on-site machining, or flange replacement—would have led to costly delays and prolonged downtime.
Instead of opting for these time-intensive repairs, the client required a custom-made gasket that could fit the damaged groove and restore functionality quickly. With our history of delivering effective solutions under pressure, we were called upon to design, manufacture, and deliver a custom gasket solution on an urgent timeline.
The moment we received the emergency call, our team quickly evaluated the situation. Working closely with the client, we developed a custom engineered gasket specifically designed to accommodate the damaged groove while withstanding the harsh conditions of a chemical environment.
By leveraging our in-house manufacturing capabilities, we were able to design and fabricate the gaskets in just a few hours. Thanks to the dedication of our production team at the Welshpool facility, who immediately got on top of the job and stayed behind to expedite the process, we had the gaskets ready by the end of the day.
Team-Driven Solutions: Delivering Under Pressure
Behind every successful emergency response is a team member who goes the extra mile—literally. In this case, it was one of our experienced KLINGER representatives Alby Vandenberg who took on the challenge under intense time pressure.
Recommendations on materials were made on the spot. Design from the engineers were done straightaway. Production began immediately. Then, it was up to Alby to set in and make the delivery – hundreds of kms away.
While many were wrapping up their week on a Friday afternoon, he was on the road to personally deliver the gaskets. This wasn’t the first time he had to taken on such an urgent task.
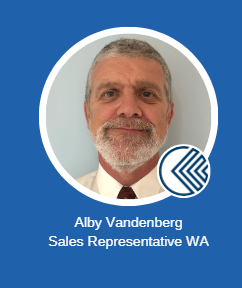
You would hope everything could be planned in advance, with plenty of notice to get things done right. But the unexpected can happen, and requests like this really tested our team’s resilience and ability to adapt under pressure.
In my 35 years with the company, this is just one of many instances where our entire team—engineering, production, and client support—has worked hard to make it happen. It often involves long hours and plenty of coordination, which can be stressful for everyone involved. But at the same time, these situations are exciting, and there's a sense of satisfaction that comes from knowing we’ve pulled together as a team to meet the challenge.
When our products are the key to solving critical problems, they become something much more. This is also why we’ve always insisted on having production plants close to our customers. Knowing that we can respond quickly in situations like this, saving significant costs that would otherwise be substantial, is what makes all the hard work truly worth it."
Alby Vandenberg, KLINGER
Get Back Online Faster
We think this is a perfect example of how tailored gasket solutions, combined with responsive service and emergency manufacturing capabilities, can prevent costly production downtime and ensure the integrity of critical equipment.
Emergencies like this can happen at any time, but having the right partner can make all the difference. Whether it’s a custom gasket design, advice on material selection, or proactive maintenance support, we’re here to provide solutions that keep your operations running smoothly.