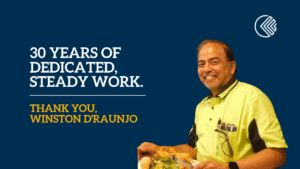
- KLINGER Australia
- Blogs
- 9 Critical Causes of Flange Leaks and How to Fix Them
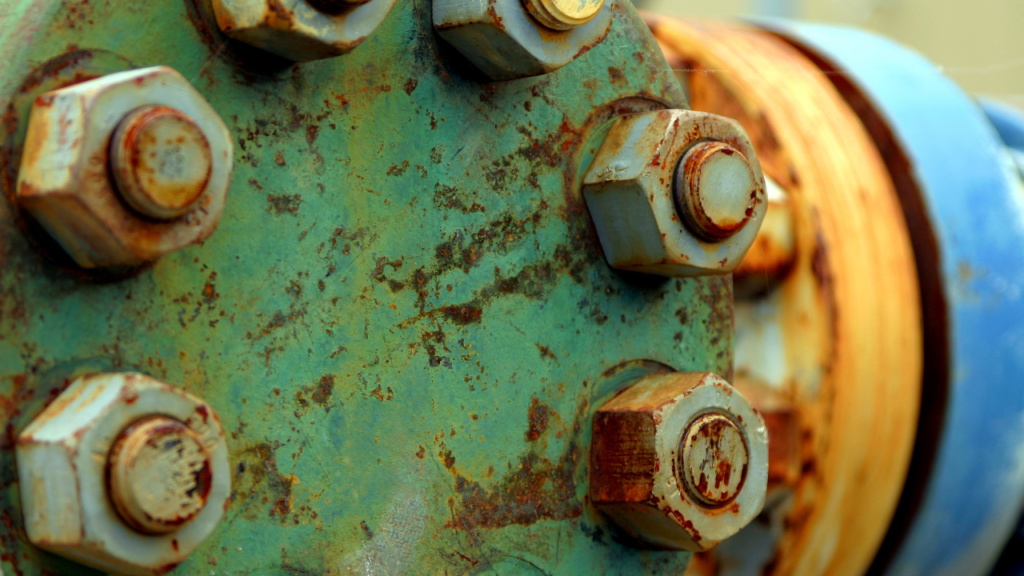
Photo credit: Canva
Flanges are crucial connecting components in pipeline systems, providing easy access for inspection, cleaning, and modification of the piping system.
Flange leaks can range from a slow emission that’s barely detectable to a sudden, drastic failure. The causes of flange joint leaks can include incorrect or inappropriate installation of fasteners or gaskets, improper selection of materials, or operational shock or stress. With the ongoing expansion of piping networks to meet rising demands for energy, water, and other resources, the concern over flange leaks is becoming even greater. Here are the guidelines on how to prevent them from stopping your operations and causing harms:
Too tight or not tight enough fasteners and uneven bolt stress
An improperly tightened assembly or loss of bolt stress over time can lead to leaks. Incorrect bolt-up procedures or limited working space around the flange can cause uneven bolt stress. Conversely, overly tight fasteners can exert excessive pressure on the gasket or increase fatigue on aging equipment, potentially leading to stress cracking. This imbalance is particularly problematic in high-temperature services, where heavily loaded bolts may relax and cause leaks.
🛠️ To prevent this, ensure that bolts are evenly tightened using the proper torque values and tightening patterns.
Improper flange alignment
Improper flange alignment, especially in terms of flange face parallelism, can cause uneven gasket compression and local crushing, leading to leaks. Misalignment of the flange centerline can similarly result in uneven gasket compression and subsequent leaks.
🛠️ Always check and correct flange alignment during installation to ensure a proper seal.
Improper flange facing and surface finish
Flanges with deeper serrations than specified can hinder the proper seating of double-jacketed, kammprofile, or spiral-wound gaskets, resulting in leakage paths. 🛠️ Always verify flange facing specifications. Refer the table below from ASME -PCC-1 Guidelines to ensure they are compatible with the gasket type.Excessive piping system loads at flange locations
Excessive forces and bending moments can loosen bolts or distort flanges, resulting in leaks. Common causes include insufficient piping flexibility, the use of excessive mechanical force alignment, and improperly placed supports or restraints.
🛠️ To prevent this, ensure the piping design includes sufficient flexibility and correctly positioned supports.
Improper gasket installation, particularly centering
When a gasket is installed off-center relative to the flange faces, it will be unevenly compressed, increasing the likelihood of leakage.
🛠️ Begin with knowledge of the correct Installation procedure.
A trained bolt-up crew should always verify the gasket specifications before installation. Specifications from your gasket manufacturer and ASME PCC-1 will be most valuable.
Spiral wound, double-jacketed, and kammprofile gaskets typically feature a centering ring that extends to the inner edge of the bolts, ensuring proper alignment.
For sheet gaskets, cut the outside diameter to match the inner edge of the bolts to ensure even compression.
Improper gasket size, material
Using an incorrect gasket size or material can cause flange leaks. The wrong size is typically noticeable during installation, whereas the wrong material might not become evident until corrosion or a blowout occurs.
🛠️ Ensure the correct gasket size and material are selected for the specific application to prevent issues. Elastomeric-based gaskets can become brittle under elevated temperatures or certain chemical conditions. If these gaskets start to leak slightly, retightening may cause them to break, potentially leading to a serious blowout. Avoid using lower-priced gaskets when possible, as performance and longevity are crucial.
Vibration levels
Excessive vibration can loosen flange bolts, leading to leakage.
🛠️ Implement vibration damping measures and regularly inspect and retighten bolts as necessary to maintain a secure flange connection.
Thermal shock
Rapid temperature fluctuations can temporarily deform flanges, leading to leaks, which is a significant concern in high-temperature applications. Temperature variations around the flange circumference, such as cooling from rain on top or differences between hot gas and cool liquid, can exacerbate this problem. Due to different rates of thermal expansion, there can be a dramatic loss of bolt stress.
🛠️ Installing sheet metal shields can protect against rain and snow, helping to maintain uniform temperatures around the flange and bolts.
Dirty or damaged flange faces
Corrosion pitting, a localised form of corrosion that leads to the creation of small holes or pits in the metal, is a common cause of flange leaks. Other contaminants such as dirt, scale, scratches, protrusions, weld spatter, and warped gasket seating surfaces, can also create leakage paths or cause uneven gasket compression, resulting in flange leakage.
🛠️ Regular inspection and maintenance, along with the use of corrosion-resistant materials and protective coatings, can help mitigate the risk of pitting corrosion and subsequent flange leaks. Always clean and inspect flange faces before installation to ensure a smooth, even surface for the gasket.
Safety at stake
Technicians must be vigilant and promptly address any obvious signs to prevent flange leaks and ensure overall safety. However, human errors can occur. Prioritising the safety of personnel and the facility is crucial for any operator, and it is essential to take every reasonable measure to ensure safety when managing potential flange leaks.
Spray shields can effectively mitigate the impact of leaks. Spray Shields, also known as flange guards, flange wraps, or flange protectors, are designed to prevent leaks from spraying over a wide area. Safety Spray Shields help avert injuries to personnel, damage to nearby equipment, and environmental harm in the event of a spray-out of hot or hazardous liquids.
KLINGER Spray Shields are high-quality protective composite jacketing. These shields are designed to address potential flange rupture leaks and deflect potential effluent to the containment bed, thereby protecting the surrounding work environment. They are weather and chemical-resistant, flexible, easy to install, remove and reinstall, allowing quick access and easy equipment serviceability.